HAZOP Technique
2025-02-09
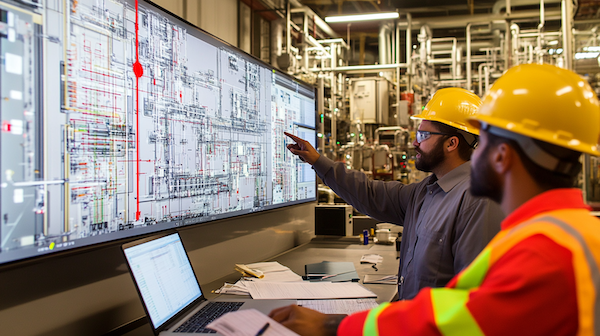
HAZOP (Hazard and Operability Study) Technique
Key Points
- Systematic & Structured: Follows a structured approach using guide words to explore deviations.
- Team-Based Approach: Involves experts from various disciplines.
- Qualitative Risk Assessment: Identifies hazards and operability issues rather than quantifying risk.
- Process-Oriented: Best suited for industrial processes and system designs.
- Focuses on Deviations: Uses guide words like "More," "Less," "Reverse," and "No" to explore potential failures.
Benefits and Limitations
Benefits
✔ Identifies both safety hazards and operability issues.
✔ Encourages cross-functional collaboration.
✔ Enhances process safety and regulatory compliance.
✔ Improves system understanding by systematically analyzing deviations.
✔ Helps in identifying potential failure modes early in the design phase.
Limitations
✖ Time-consuming and resource-intensive.
✖ Heavily reliant on the expertise of the team.
✖ Does not provide quantitative risk assessment.
✖ May not effectively capture all possible hazards if guide words are applied incorrectly.
Introduction
The Hazard and Operability (HAZOP) Study is a well-established technique used to systematically evaluate potential hazards and operational issues in industrial processes. Originally developed in the 1960s by Imperial Chemical Industries (ICI), HAZOP has become a standard method for risk assessment in industries dealing with hazardous materials and complex systems.
The technique relies on breaking down a process into manageable sections (nodes) and analyzing potential deviations using predefined guide words. These deviations help uncover hazardous conditions and operability problems that could lead to accidents, system failures, or inefficiencies.
How HAZOP Works (Theory & Methodology)
1. Process Breakdown into Parts/Nodes
The system or process under analysis is divided into functional sections called parts. Each part represents a segment of the process where a specific operation occurs, such as a reactor, a heat exchanger, or a storage tank.
2. Application of Guide Words
Guide words are applied systematically to process parameters (e.g., flow, temperature, pressure, level) to explore possible deviations.
Common Guide Words and Their Meanings
Guide Word | Meaning | Example Deviation | Potential Hazard |
---|---|---|---|
No / Not | Complete absence of the intended function | No flow in a pipe | Blockage or pump failure |
More | Higher than expected parameter value | Excessive pressure | Over-pressurization leading to explosion |
Less | Lower than expected parameter value | Insufficient cooling | Overheating causing thermal runaway |
As well as | Presence of an unintended element | Contaminants in a process stream | Product quality degradation |
Reverse | Opposite of the intended action | Reverse flow in a pipeline | Cross-contamination or pump damage |
Other than | A completely different event occurs | Wrong material in a tank | Safety or quality hazard |
3. Identifying Causes and Consequences
For each deviation identified, the team investigates:
- Possible Causes (e.g., equipment failure, human error, design flaw).
- Potential Consequences (e.g., fire, explosion, product loss, environmental impact).
4. Safeguard Analysis
Existing safeguards such as alarms, relief valves, interlocks, and operator interventions are evaluated for their effectiveness in preventing or mitigating hazards.
5. Recommendations for Improvement
If safeguards are inadequate, the team proposes additional control measures such as design modifications, procedural changes, or enhanced monitoring systems.
Real-World Applications of HAZOP
1. Chemical Processing Plants
- Used to identify risks in reactor operations, piping systems, and storage tanks.
- Helps prevent dangerous chemical reactions, over-pressurization, and leakages.
2. Oil and Gas Industry
- Applied in refineries, offshore platforms, and LNG facilities to assess pipeline flow deviations, pressure build-ups, and equipment malfunctions.
- Ensures compliance with safety regulations such as OSHA and API standards.
3. Pharmaceutical Manufacturing
- Ensures that deviations in ingredient mixing, sterilization, and packaging do not lead to quality or safety issues.
4. Water Treatment Plants
- Evaluates risks in filtration, chemical dosing, and distribution systems to prevent contamination.
Step-by-Step Guide to Conducting a HAZOP Study
Step 1: Define the Scope and Objectives
- Determine which system, process, or facility will be analyzed.
- Set objectives based on regulatory requirements, safety goals, or design reviews.
Step 2: Assemble a Multidisciplinary Team
A HAZOP study team typically includes:
- Chairperson (Facilitator): Ensures the study follows the methodology.
- Process Engineers: Provide technical details about the system.
- Operators: Offer practical insights into daily operations.
- Safety Experts: Assess risks and safeguards.
- Instrumentation & Control Engineers: Evaluate automation and interlocks.
Step 3: Break the System into Parts/Nodes
- Divide the process into logical sections (called parts/nodes) such as equipment, piping, or control loops.
- Use Piping and Instrumentation Diagrams (P&IDs) to define parts clearly.
Step 4: Apply Guide Words to Identify Deviations
- Select a process parameter (e.g., pressure, temperature, flow).
- Apply a guide word (e.g., "More" → More Pressure).
- Identify potential causes and consequences of the deviation.
Step 5: Assess Existing Safeguards
- List safety measures (e.g., alarms, relief valves, operating procedures).
- Evaluate if safeguards effectively prevent or mitigate the hazard.
Step 6: Recommend Improvements
- Propose additional safety measures, process changes, or training.
- Document findings in a HAZOP worksheet for review and implementation.
Step 7: Review and Follow-Up
- Present findings to management for decision-making.
- Implement approved recommendations and verify effectiveness through audits or follow-up reviews.
Further Reading
- IEC 61882:2016 – International standard for HAZOP methodology.
- CCPS Guidelines for Hazard Evaluation Procedures – Center for Chemical Process Safety.
- OSHA Process Safety Management (PSM) Standard (29 CFR 1910.119) – Regulatory framework for hazardous processes.
- Complement HAZOP with the HAZID technique to find hazards from outside the process.
Contact Us for HAZOP Expertise, Training, and Certification
Need a HAZOP Expert?
Looking for HAZOP Training?
Register here: HAZOP and HAZOP Leadership training
Want to Become a Certified HAZOP Leader?
Get started here: HAZOP Leader Role Certification